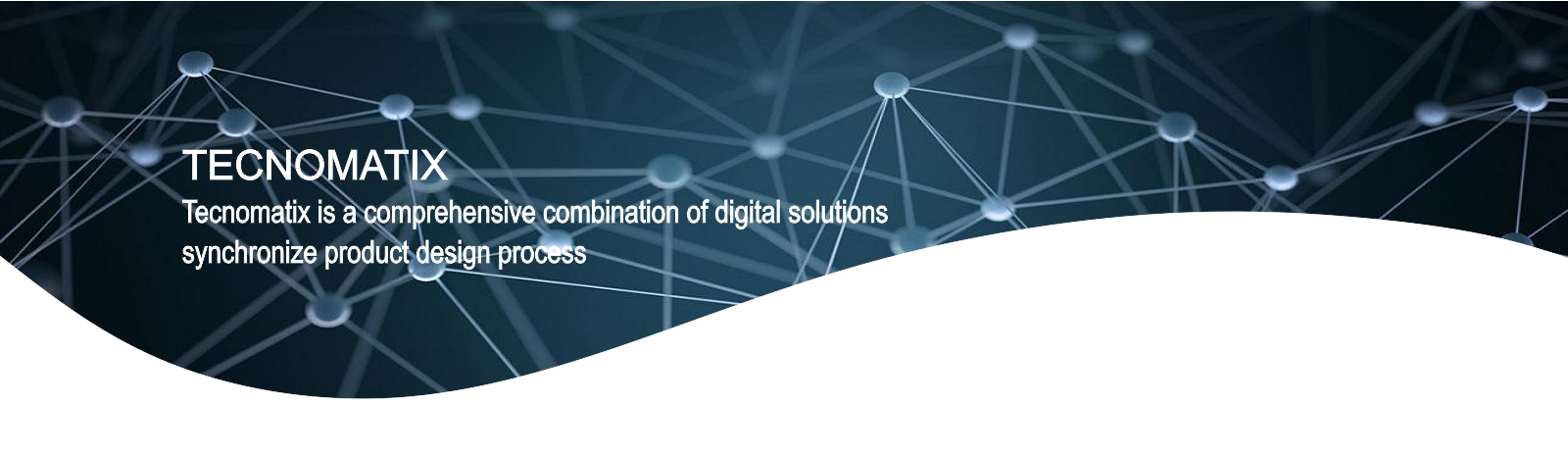
TECNOMATIX
Tecnomatix is a comprehensive portfolio of digital manufacturing solutions that help you realize innovation by synchronizing product engineering, manufacturing engineering and production. Supported by the best-in-class Teamcenter Manufacturing PLM platform, Tecnomatix provides the most versatile set of manufacturing solutions on the market today.

Increased Planning Productivity
- Reuse certified processes and reduce capital equipment costs by capturing and managing within a single source of manufacturing knowledge.
- Detect and eliminate problems within production systems that would otherwise require time-consuming and cost-intensive corrective measures during production ramp-up.
- Reduce assembly planning tasks, planning time and their associated costs.
- Sharing and analyzing information within a digital environment provides insight into the various stages of process development and the impacts of those processes.
- Streamline communications so you can adapt to customer demands quicker, with decisions based on facts.
Optimized Manufacturing Productivity
- Minimize capital investment and maximize long-term ROI through increased planning accuracy and efficiency.
- Shorten time-to-volume production through the analysis of product manufacturability and process development.
- Optimize the logistics and performance of entire production systems.
- Optimize resource utilization and accelerate product launches with proven solutions for process optimization that cross multiple departments and disciplines.
- Benefits
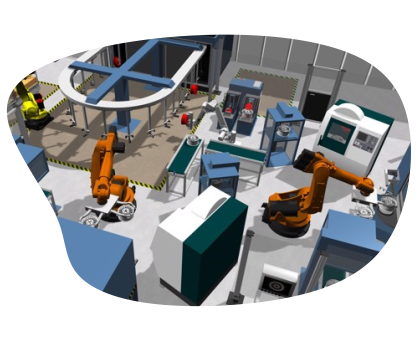
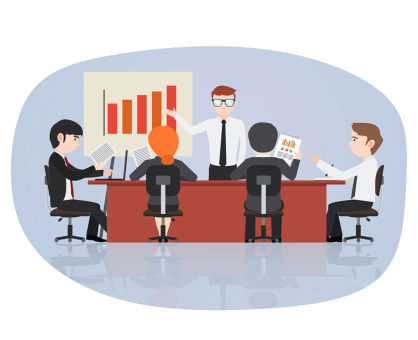
Increased Plant Productivity
- Program information is available at all levels of the enterprise – from executive to plant floor personnel.
- Achieve smaller launch windows, increased plant capacity and material cost control through comprehensive visibility into quality issues.
- Reduce capital investment costs via commonization and reuse.
Single Source for Alignment and Accountability
- Assembly and manufacturability validation provides accelerated feedback to design and process teams.
- BOM/BOP configuration and management reduces planning errors by ensuring all components of a product are accounted for and aligned.
- In-context collaboration and communication operate globally within the supply chain networks by coordinating workflow processes ensuring timing is maintained.
- In-context collaboration and communication of workflow processes ensures that timing is extended throughout the global supply chain.
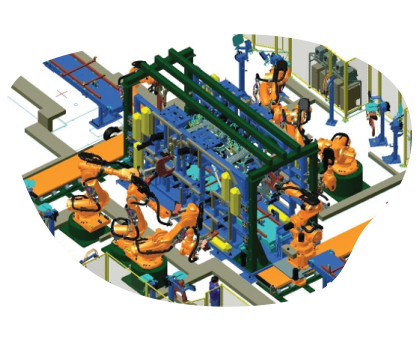
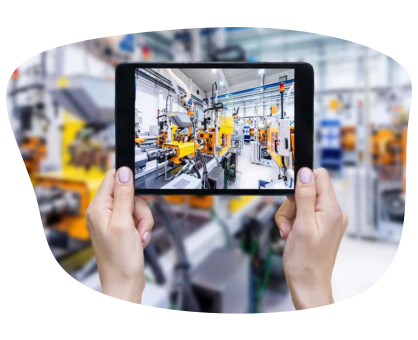
Optimize Performance & Leverage “Best Practice” processes
- Reduce process development time up to 40% by identifying and applying best-in-class processes with master process and operation templates.
- Achieve 20-to-80% reuse of certified manufacturing processes within the first year.
- Significantly reduce and even eliminate production disruptions caused by manufacturing shop floor issues, by balancing processes for optimum value added content.
- Optimized manufacturing lines through virtual commissioning to reduce time-to-volume by up to 80%.
Managed Environment for Safety and Ergonomics
- Reduce corporate liabilities and expenses for worker related injuries.
- Eliminate hazardous work environments by integrating ergonomic simulation and validation into the development process.
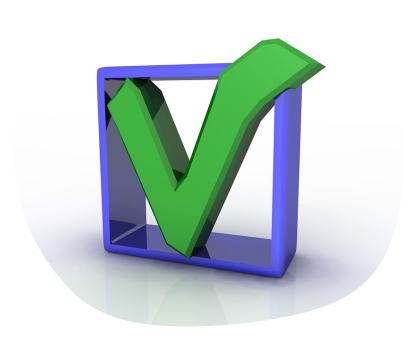
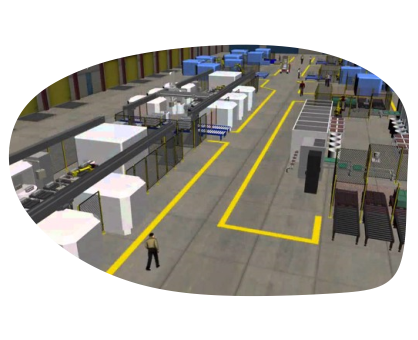
3D Factory Design and Visualization
- Reduce factory design time, from concept through installation, by up to 50% when compared to traditional 2D design methods.
- Reduce tooling and equipment changes 15% by discovering design flaws and issues early in the creation phase, as opposed to later in the installation phase.
Factory Logistics Analysis and Optimization
- Reduce material handling costs up to 70% by analyzing cost, time, and travel distances across multiple factory layouts.
- Optimize space utilization at both the plant and transportation truck level by analyzing and evaluating material requirements, container sizes, container stacking criteria as well as ingress/egress guidelines.
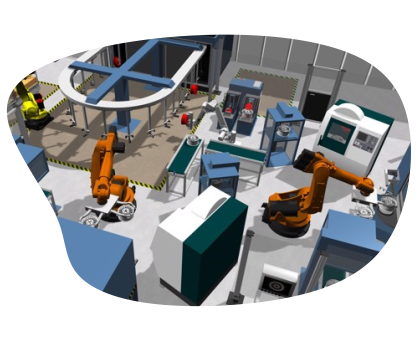
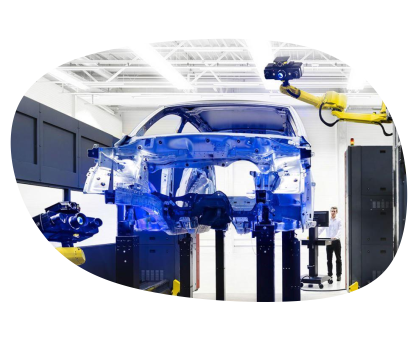
Factory Production Throughput Simulation
- Reduce throughput time as much as 20-60% by taking into consideration internal and external supply chains, production resources, and business processes.
- Increase productivity for existing systems 15-20% with easy to interpret statistical analysis.
- Decrease new system costs 5-20% by detecting and eliminating problems before having installed the real system.
- Reduce inventories 20-60% by evaluating different line control strategies as well as verifying synchronization of lines and sub-lines.
Block "3768" not found